by Jeremy Hodgkinson FSA
At their simplest, firebacks are cast-iron plates intended to be placed at the rear of fireplaces with the twofold purpose of protecting the material from which the fireplace has been constructed, be it wattle and daub, stone or brick, and reflecting the heat of the fire into the room. In their plain, unadorned state they are very easy to produce, requiring the preparation of a shallow, level depression in casting sand into which molten iron can be poured.1 Because this forms an open mould, firebacks produced in this way have decoration on only one side. They were robust, slow to corrode and relatively cheap.
From the outset firebacks were made at blast furnaces, where cast iron was produced by smelting iron ore. The iron from such furnaces was normally cast into large ingots called sows or pigs for onward transport to forges where they would be refined into wrought-iron bars. It was a simple matter, therefore, to prepare a different shaped open mould to cast a flat plate instead. With the introduction and spread of foundries, where iron pigs made at blast furnaces could be remelted and cast into a variety of forms, it is probable that many later firebacks were produced in urban locations.
A contemporary description tells us:2
…as for the backs of Chimneys, Garden-rolls, and such like; they use a sort of cast-Iron which they take out of the Receivers* of the Furnaces, as soon as it is melted, in great Ladles, and pour it into moulds of fine sand in like manner as they cast the other softer Metalls.
*i.e. Reservoirs
Firebacks were usually cast in open sand moulds, the ‘green’ sand being naturally bonded with a small percentage of clay to give it pliability at the stage when the mould was being prepared but harden subsequently to hold the shape of the pattern pressed into it when the iron was poured. A flat bed of casting sand would have been prepared, ideally with a level surface though examples where one or more edges vary in thickness from the others are not uncommon. Onto this would have been placed a board of the desired shape for the fireback. This may have been a single plank of wood in the case of a small fireback, or a series of planks battened together for a larger one. The simplest firebacks were rectangular, but boards could be made to other shapes, the most popular of which included a central arch above the rectangle, a form popularised by the architect Andrea Palladio.
The board would have been tamped down to leave a firm sand depression, or mould, into which the decoration could then be impressed. A pouring basin might have been formed on one side in the sand adjoining the mould to allow the iron to flow into the mould. After removing the base board, decorative elements, which may have been everyday objects, or specially carved stamps including letters and numbers, would be arranged and pressed into the sand. The arrangement would have to be made as a mirror image of the intended design, an aspect of the preparation of the mould which may have been the cause of confusion to some of the less literate workers involved when it came to arranging letters and numbers.
Use of whole carved wooden patterns, or models, simplified much of the foregoing process. As the pattern would be identical in size and shape to the finished fireback, all that was necessary to do was to firmly press the pattern face down into the sand to form the mould. The design on the surface of the pattern, which would have been carved as it would appear on the surface of the fireback, would naturally form a negative image in the sand. Only five English fireback patterns are known to have survived.
With the laying out of the decoration complete, the sand would have been allowed to harden before the molten iron was poured in. Generally this next stage in the process would have been undertaken by ladling iron from the forehearth of the furnace and pouring it either directly or indirectly into the mould. Iron poured directly onto the mould could result in the sand/clay mixture from which the mould was made being displaced by the impact, resulting in a depression, and a slight mound on the surface of the casting which might obscure some of the decoration. Evidence of this occurrence can be seen on several firebacks (Fig. 1).
Pouring the iron indirectly into a shallow basin to the side of the mould, allowing the molten metal to run into the mould horizontally, removed that risk though a residual lump of iron at the side of the casting might result from the runner, where the iron entered the mould, being knocked off (an example can be seen on Fig. 2). In the case of very large firebacks, a channel may have been formed between the furnace and the mould, and the iron allowed to run directly from one to the other. As the iron cooled in the mould, sand was sometimes spread lightly onto the upper surface of the molten iron to slow down the cooling process, resulting in a pock-marked appearance on the reverse side of the fireback.
The first area in Britain where blast furnaces were employed for iron making was the Weald of south-east England, and this region, which incorporates parts of the counties of Sussex, Kent and Surrey, was to remain the principal producer of cast iron in Britain until the middle of the seventeenth century, the most productive period for the manufacture of firebacks. The earliest furnaces there dated from the last decade of the fifteenth century and iron production, including that of firebacks, continued until 1813.3 From the 1560s, however, blast furnaces were established in other parts of Britain, such as the Forest of Dean in Gloucestershire, South Wales, the north and west Midlands and Scotland. Later, iron casting spread to Furness in what is now Cumbria where, in 1744, John Lucas noted that at Leighton Beck Furnace the Backbarrow Company produced chimney backs among other items.4
The locations of blast furnaces, any of which would have been capable of producing firebacks, have been documented by historians, though actual accounts of production have survived for only a relative few. Urban foundries have been harder to identify as their archaeological imprints have been more fleeting and their operational histories more transient. Foundries did not require the elaborate water-management systems that blast furnaces needed, nor did they produce the large quantities of waste slag by which blast furnace sites can be identified.
Firebacks, Stove-plates and Taques de foyer
While only firebacks were produced in Britain, some iron plates of continental origin, which have been imported into Britain and used as firebacks, were originally designed for a different but related purpose. In the Eifel region of Germany, and later in Scandinavia and colonial North America, iron stoves were made, and when these were dismantled because of wear or disuse the individual plates from which they were assembled, and in particular those from the sides, could be substituted for firebacks as they were of similar material and size, and often vividly decorated (Fig. 3). They can be identified by their flanged edges and sometimes narrow proportions.
In the southern part of modern Belgium and the adjoining area of France, Luxembourg and Germany, in the regions known as Wallonia and Lorraine, decorated iron plates identical to firebacks were used as partitions behind fireplaces to serve as radiators of heat into an adjoining room. These were known in French as taques de foyer and in German as takenplatten, for which an English translation might be ‘covered plates’ (Fig. 4).
A rare and unusual form of English fireback is a free-standing type which incorporates two forward-facing ‘wings’, one on each side and perpendicular to the main panel, which widen towards the base to provide stability. The intention of these small firebacks would seem to be to provide a heat-reflective backing for a fire located in an otherwise open location, where a suitable surface such as a wall was not available. Three of the four examples that have been noted are decorated with a tree or plant motif, and two have inscriptions though these are no longer legible. While not identical in other respects, the same three are surmounted by panels decorated with a crown between two animals, possibly a lion and unicorn (Fig. 5).
In the early Middle Ages, domestic fires had been located in the centre of the open hall, with chimneys being constructed only in high-status buildings. The incorporation of chimneys into domestic buildings in England, by which floors and heated rooms could be distributed throughout houses, was consequent upon the greater availability of suitable building material, such as brick and stone. They were preceded by the smoke hood and smoke bay, which were constructed of the same materials as the rest of the house – in south-east England, timber framing with wattle-and-daub infilling. The inherent dangers of enclosing a fire within a structure made of flammable materials points to the development of such structures being facilitated by the availability of protective iron plates which newly established blast furnaces could produce. It may be no coincidence that the development of domestic chimneys and the introduction of cast iron occurred at around the same time. A demonstrable need may well indicate when firebacks were first likely to have been made in England. In the south east, smoke hoods and bays did not begin to be built until about 1510 in rural areas,5 a fact which may have been influenced by the availability of cast-iron plates. The change-over continued in the region until about the 1560s, and the need for exceptionally wide firebacks, to protect large areas of insubstantial, internal wall exposed to domestic fires may have been particularly strong until around that time.
Although firebacks are widespread in Britain, and particularly in the South East and in the west Midlands, the production of copies and the dispersal, in the past decades, of many examples from the houses where they had been for centuries, means that it is not easy to assess their former distribution.
Firebacks in Inventories
Firebacks sometimes feature in the inventories that were drawn up to list the possessions of people shortly after they had died, or for other reasons. In inventories they are most commonly described as iron backs or simply backs. Sometimes they are termed plates although with plates for food also appearing in inventories, and plate also referring to silver plate, resolving such ambiguity will depend on the context in which the word plate is used. Inventories vary considerably in the amount of detail they provide and brief, summary inventories employing phrases such as ‘all the ironwork’ could conceal the presence of a fireback. Backs may not have been recorded in some probate inventories if they were regarded as fixtures. Just such a case is the 1664 inventory of John Tufton, the second Earl of Thanet, who lived at Hothfield in Kent. In it the appraisers specifically noted rooms where firebacks, and other items including window shutters and some pictures, were not to be valued because they were fixed.6 The distribution of firebacks across Britain will have been governed by several factors, proximity to an iron production area and the availability of fire-resistant house building material probably being the most common. The frequency of the inclusion of firebacks in inventories is likely to reflect such distribution The nine properties where ‘backes of iron’ were recorded in the second half of the sixteenth century in inventories in Exeter, Devon, a city not particularly near to an iron production area, is clear evidence of their distribution.7 However, such distribution was variable. Out of 72 inventories of residents in Ipswich, Suffolk, between 1583 and 1631, only one mentioned a fireback, and there was nothing about the rest to suggest that the presence of firebacks had been subsumed into collective entries for pieces of ironwork.8 In a group of 90 inventories that have survived of people living in the parishes of Ifield, Crawley and Worth, in Sussex, eleven houses out of the 74 inventoried between 1662 and 1729 were recorded as having iron plates or iron backs – nearly 15 percent,9 while of 79 inventories from the parish of Ledbury, Herefordshire, between 1662 and 1700, only five houses are recorded as having firebacks – just over 6 percent.10 The Sussex parishes lay in an iron-producing region at the time, but Ledbury lay less than 20 miles from some of the furnaces in the Forest of Dean. A wider survey, undertaken by the author, of probate inventories compiled in the diocese of Gloucester between 1651 and 1700 noted that out of 6,099 inventories only about three percent mentioned one or more firebacks and the diocese included the significant iron production area of the Forest of Dean. In none of the inventories were details recorded which could help in identifying the firebacks concerned. Indeed, descriptions of the decoration are extremely rare. One such, from Southampton in 1558 noted ‘A yrren bake wth the Inglyshe Armes’ valued at 2s 6d.11
A particularly early inventory to include firebacks is that of William, 1st Baron Sandys, of The Vyne in north Hampshire, who died in 1540. In the scullery and kitchen of his house are listed ‘1 large payr of backs of Yron’ valued at 40 shillings, ‘A payr of lesser backs’ at 26s 8d and ‘A payr of smaller backs’ at 13s 4d.12 The valuation given for them, which was substantially higher than for firebacks in inventories two or three decades later, perhaps gives an indication of their then relative rarity and/or cost of cast iron.
A different sort of inventory was compiled following the bankruptcy of Robert Baker in 1708. He was the ironmaster of Hamsell Furnace and Birchden Forge at Rotherfield in Sussex and, in addition to a fireback noted in the furnace house at Hamsell, 22 iron backs with a combined weight of five hundredweight, and evidently products of the furnace, were in the custody of a local man, John Harrison. Their average weight was only about 25 lb. This was very light for firebacks and suggests that they might have been of the Dutch style, which are known to have been cast thinner and lighter than the indigenous types.13
Unsurprisingly, major landowners in iron-producing areas made extensive use of firebacks in their homes. Following the death, in 1632, of Henry Percy, the ninth Earl of Northumberland, an owner of ironworks, the inventory of his chattels listed 21 firebacks in his mansion at Petworth, Sussex, including ‘a lardge yron backe’ in the hall.14 It is likely that some of the early 17th-century firebacks still in Petworth House (see Figs. 6-8) may have been included in that number. Distance from the source of firebacks, however, was no problem if you were rich enough. When the Crown sued Adam Baynes for the recovery of Holdenby ‘Palace’ in Northamptonshire after the Restoration, among the list of items sought were 50 iron chimney backs. Holdenby had been completed in 1583 for Sir Christopher Hatton, Elizabeth I’s influential courtier and favourite and was, in its time, the largest privately-owned house in England.15 Whether the firebacks were purchased as a single order from one ironworks or assembled piecemeal will probably never be known. Holdenby was at least 60 miles from the nearest furnace.
We do know the source of a large order of firebacks for Boughton House, also in Northamptonshire. Its owner, the 2nd Duke of Montagu, had inherited the Lordship of Furness, at the southern end of the Lake District, which included extensive resources of iron ore. Among the leases granted for the extraction of ore were several to Richard Ford who established iron furnaces at Low Nibthwaite and later at Newland.16 In 1743 it was with Ford that a contract was placed to supply 50 firebacks for Boughton. They were cast in sizes to fit specific fireplaces in the house and each was decorated with one of five identical but differently sized designs of the shield, Garter and coronet of the duke, according to the size of the plate (Fig. 9). Totalling seven tons they were delivered in two batches by sea to King’s Lynn in 1748 and carried up the River Nene to Thrapston, from where they were carted to Boughton.17
There are occasional other references to the existence of firebacks, such as the record of the need to repair a chimney back in the Lord Treasurer’s office in 1556.18 Presumably it had been there for some time. Christy mentions an iron back in the Great Gallery of Lambeth Palace in 1575, and another in the old parlour of the Lord Mayor of London, Sir Thomas Ramsay, in 1590.19
Firebacks in Wills
Firebacks occasionally featured as bequests in people’s wills. This tended to be the case among the less wealthy where the property to be distributed mainly consisted of household items rather than money or land. The earliest recorded to date are those of William Shepard of Heathfield in Sussex, who left his four iron plates to his two sons in 1546, and James Bramlay of Frant who in 1549 left his plate to a friend.20 In 1557 Thomas Darell of Scotney Castle in Sussex bequeathed to his wife Alice “the backs of Iron for too chimneis”,21 and in the following year John Haywarde of Hartfield, in the same county, had instructed his executors that “the plate in the chimney in the hall … shall remain at the same house during my lease and term of years”.22 Similarly John Cogan, a merchant of Chard in Somerset, was most particular about his possessions, including the backs in his chimneys, when he left them to his wife for the rest of her life in his will of 1590. When she died she was to leave the backs, amongst all his other chattels, in the house for his heirs.23 And in 1652 Henry Hilder, a yeoman of Withyham, Sussex, had bequeathed “as a remembrance … one yron plate in or near the chimney in the house wherein I now dwell” to his friend, Thomas Rivers, who was expected to pay twenty shillings to his executrix on its delivery.24 In 1653 a wealthier testator, Peter Farnden of Sedlescombe, himself an ironmaster, willed that his “chimney backs, fire shovels, tongs, tables, forms chairs &c.” should go to the next owner of his house.25 In Suffolk, Luke Curtis, gentleman, of Bury St Edmunds left “one Iron backe” to his son, also Luke, in his will of 1680.26 Evidently bequests of firebacks were not necessarily of a personal nature. In 1696, William Hawkins, a corder, of Cugley, near Newent in Gloucestershire, left to his niece “the Cast Iron back in the Chymney or Twenty Shillings to be paid for the same by my said Nephew John Hawkins”.27 Out of the 197 people in the diocese of Gloucester between 1651 and 1700 in whose inventories of their property one or more firebacks were itemised only 17 left wills in which they were specifically bequeathed – just over eight percent.
Firebacks and Graveslabs
Similar in many respects to firebacks are cast-iron graveslabs, which are found in many churches in the Weald, and a few in the west Midlands and Yorkshire.28 There are strong parallels between firebacks and graveslabs. Probably the earliest graveslab made of cast iron is to be seen in the parish church at Burwash, Sussex. Earlier writers attributed it to the fourteenth century because of the Lombardic lettering of the inscription, but it is now generally accepted as dating from the 1530s.29 The earliest dated graveslab, which is in East Grinstead church, is of 1570, somewhat later than the earliest dated firebacks. Like them, production of graveslabs lasted in the Weald until the end of the eighteenth century. The manufacture of the two products was virtually identical, with only two graveslabs of members of the Still family in Cowden churchyard in Kent, and a brass-inlaid memorial to Judith Legas, in Wadhurst, Sussex, likely to have been cast in a different way to the open, sand-casting method normally employed for making both backs and memorials.
The greater predominance of textual inscriptions on graveslabs gave rise to both pre-carved text stamps and the use of sets of individual alphabetical stamps. Both forms, however, fell prey to the reversal and inversion of letters, the inevitable effect of what must have been a largely illiterate workforce, at least in the Tudor period.
Instances of the use of the same stamps on both firebacks and graveslabs are relatively, and perhaps surprisingly, uncommon.
Re-use of armorial stamps has occurred in the Weald, with the Fowle family making repeated use of the stamps bearing both their arms and their crest on graveslabs in Wadhurst and Frant and on firebacks (Fig. 10), and an armorial stamp of the May family on a fireback of 1702 at Pashley Manor, Ticehurst, has also been used on an un-named and undated graveslab in the parish church (Fig. 11).
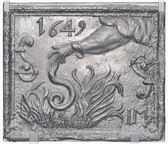
The work of the same pattern-maker can sometimes be recognised on both firebacks and graveslabs. Particularly clear is the style of lettering and numerals on the graveslabs of three members of the Bucher family buried in Wadhurst church between 1638 and 1640, which bears the unmistakable hand of the carver of patterns for a number of firebacks of the same period, and whose initials are likely to be the ‘IM’ on several of them (e.g. Fig. 12).30
A different, but nevertheless distinctive style can be discerned on both a small fireback, dated 1776, at Scotney Castle, Kent, and on the graveslab of John Wells Luck and Ann Luck, of five years earlier, in Wadhurst church porch (Fig. 13).
Most unusual has been the re-use on firebacks of epitaphs from graveslabs. The earlier of the two instances is that of Richard Graye, rector of Withyham in Sussex, who died in February 1582 (Old Style). The iron slab over his grave in the choir of his parish church bears an inscription in relief. Two firebacks have been recorded with the same inscription, which was evidently carved on a board in sans-serif lettering: one is now in the church (Fig. 14), while the other, formerly at Wolvesey Palace, Winchester, and later in the city’s museum, is lost.
The second, and probably better known, instance concerns the carved inscription used in the preparation of the mould for the graveslab of Anne Forster at St George’s church, Crowhurst, Surrey, nine years later. At least 13 firebacks have been recorded with the identical epitaph, all of different sizes and some with more decoration than others. The wording explicitly claims Anne Forster’s right, and implicitly that of her children, to their inheritance from her father, and for this reason it seems most probable that the firebacks were cast for her family to distribute in memoriam, in support of that claim (Fig. 15).31
Fireback Manufacture and Trade
The earliest reference to ‘iron plates, for chimneys’ in England is in the imposition of a poundage charge per dozen levied by the sheriffs of Bristol c.1519.32 Whether these were imported from abroad or brought into the city from elsewhere in Britain is not known. In a long list of towns of origin that were exempted it may be significant that the Cinque Ports, among which were the Wealden towns of Hastings, Winchelsea and Rye, were included. The earliest documented production of firebacks in England is the reference to four ‘plates for Chymneys’ cast at Worth Furnace, Sussex, in 1547-8, at 3s 4d each.33 However, from the evidence of wills, noted above, it is highly unlikely that this was the earliest date at which firebacks were made.
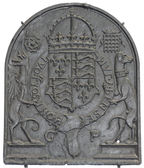
A casting of a highly sophisticated pattern, dated 1548, showing the arms of Edward VI has been noted in Berkshire (see Fig. 16). Schubert drew attention to this particular design, citing other examples in Düsseldorf, in Germany, and Arlon, in Belgium.34 Both of those had been in Belgian collections, and although similar examples are to be found in England, including a fine but undated variant in the Victoria & Albert Museum (Fig. 17), other variants, some dated as late as 1606, are to be seen in continental collections.35 What sets these examples apart from other English armorial firebacks, however, is the form of the crown, which is distinctly un-English. The English royal crown has always been shown with alternating fleurs-de-lys and crosses pattée around the top of the rim, but on these firebacks there are leaves instead, or occasionally fleurs alone. Also, the style of the dragon and greyhound supporters is untypical of normal Tudor iconography. The existence in continental collections of other firebacks depicting European royal arms, apparently designed by the same pattern-maker, however, suggests that the pattern, at least, could have been made outside the British Isles.36
Discounting that group of backs, the earliest dated British fireback is a royal armorial of 1553 (Fig. 18) which bears the initials ER for Edward VI, and the inscription, MOLLAND. This was the name of a manor in north Devon that belonged to the Courtenay family, earls of Devon, suggesting that the fireback was an early example of one made to order. A similar fireback, without the inscription, was illustrated by Llewellin.37 Both firebacks were first noted in locations in the west of Britain in the first half of the nineteenth century and Llewellin suggested that the example he recorded might have been cast in South Wales, where it had first been noted. The earliest continental firebacks and stove plates date from the fifteenth century,38 so there is no reason to suppose that firebacks could not have been cast in England from as early as the construction of the first recorded blast furnace in the 1490s.
Evidence of the importation of firebacks from the Low Countries in the 1560s, perhaps of the very fireback referred to above (Fig. 16), suggests that demand was outstripping supply. A probate inventory from Southampton in 1566 included ‘a Flemishe backe of iron for the chiminy’ valued at 2 shillings.39 Between December 1567 and the following June, 230 chimney backs were shipped into London from Antwerp.40 Backs for chimneys were also among the goods that sixteenth-century merchants in Exeter brought from the Low Countries.41 With native iron output devoted largely to the national supply of bar iron, production of firebacks would not have been the principal product of the new furnaces in the Weald. A few decades later, in the first part of the seventeenth century, the situation had changed and firebacks were being exported from England. Devoid of their own means of casting iron for a further decade, 10 firebacks were sent from London to Massachusetts in March 1634 as part of a regular shipload of supplies for the growing New England colony.42 In Virginia the absence of a successful capability to cast iron continued for even longer. In 1684, William Fitzhugh, who had emigrated there from England more than ten years earlier, wrote to John Cooper, a London merchant, asking him to send by ship ‘two indifferent large Iron backs for Chimneys’.43 And in 1649 a fireback had even been delivered to Barbados by a ship from Southampton.44
Notwithstanding the possibility, noted earlier, of firebacks being cast in South Wales in the 1550s, by the 1580s their manufacture was under way in other new iron-making areas away from the Weald. At Rievaulx Furnace in Yorkshire ‘plates for the back of a chimney’ were being cast in 1583.45 In some instructions drawn up in 1590 for the operator of the furnace on Cannock Chase, in Staffordshire, the unnamed author counselled the need to account for any firebacks made there, and presumably not to ignore their casting as being too trivial.46 Schubert noted that chimney backs cast at Kilmackoe Furnace in County Waterford, Ireland, in 1612 were being sent to an ironmonger in London.45 There is even the suggestion that a venture to make cast iron at one of three furnaces set up beside Loch Maree in Wester Ross in Scotland, in the early seventeenth century, produced a fireback. The ‘back of a grate marked S G Hay’ (Sir George Hay, the principal entrepreneur of the works) was reported in an early travel book.47
In 1633, John Browne, the Kent gunfounder to the Crown, wrote to Secretary Coke acquainting him of the national interest in supporting the English gun-founding trade, which he claimed was being undercut by Swedish producers. England, he asserted, had pioneered the casting of iron ordnance and had subsequently enjoyed a healthy trade among its friendly neighbours. But that commerce had been affected to the extent that Browne’s ability to sustain his gun foundry to supply the Crown’s needs in times of national emergency would be compromised if business was not placed in his way to keep his furnace in blast. Accordingly Browne proposed that he be granted a patent for the sole production of iron pots, kettles, backs for chimneys, salt pans, soap pans, pitch pans, iron weights and other cast-iron goods, ‘according to the French manner the invention and Skill of which Manufactory [he] brought into [the] Kingdom at his charge and loss of £1000’.48 When he formally presented his petition in March 1635, the Commissioners for the Ordnance were asked to consider the proposals. While concerned at the creation of a monopoly, they nevertheless felt the overriding priority was the protection of employment and the skilled workforce. It was noted that ‘the making of the premises after the English manner is of small consideration There being made and vented thereof scarce Ten Tons per Annum’. It was also noted that a small quantity was being made in England by Walloons and other foreigners, but that the rest were imported from ‘high Dutchland’ (Germany), the quantity not amounting to more than £20 a year.49 The commissioners duly reported the following July, recommending that Letters Patent be granted.50
John Browne’s clear statement that he was seeking the monopoly of the manufacture of cast-iron goods in the French manner, as opposed to the English, may explain why the patent that he was duly granted appears to have had no appreciable effect on the production of firebacks at the time, there being no observable uniformity of style or design of firebacks after 1635 that might suggest they were the work of a single producer. However, that others were adopting the French methods that Browne claimed to have introduced is evident in an appeal made to the Privy Council in 1639. It alleged that John Hannis, ironmaster at Bishopswood Furnace, Gloucestershire, together with his founder, George Williams, were making ‘great quantities of Iron cast manufactures’, contrary to the patent granted by the King, and were inciting others to do the same. William Shingleton, of Gloucester, was promising to cover the fines, to the tune of £500, of any that would challenge Browne’s patent, and William Little was named as one of several others said to be carrying on the same practices in the wider area of the Forest of Dean.51 Evidence from the following century of the methods used in France to cast firebacks suggests that the French method was no different to that used in England, and that John Browne’s claims may have applied more to the other cast goods he cited than to firebacks.52 Nevertheless, this was a concerted attempt to challenge the patent and bring about a confrontation on the restraint of trade that Browne’s monopoly was felt to be imposing. The distinction between the French and English methods may not have affected the production of firebacks to any appreciable extent, the main products covered by the monopoly probably being pans and pots. Before long the issue would become sidelined by the descent into civil war.
The variety of firebacks that have survived from this period suggests that their production was something that many ironmasters found to be a useful source of income. The new furnace at Parkend, Gloucestershire, built in the 1650s, initially concentrated on ironwork for the shipbuilding trade on the River Severn and round shot for the Office of Ordnance, but late in the decade the ironmaster, John Wade, sold some five tons of chimney backs and baking plates at £12 a ton, all of which were sent to Bristol.53 The accounts of the Foley Ironworks Partnership, which operated several furnaces and forges in the Forest of Dean and the Severn valley, reveal a modest production of firebacks on average in the period from 1692 to 1717 but with sometimes more than 30 backs being produced in single years at the furnaces at Bishopswood near Lydbrook and Elmbridge at Newent.54
Evidence of the private market for firebacks comes in the form of a note in the journal kept by Giles Moore, the rector of Horsted Keynes in Sussex.55 In November 1657 he recorded paying thirteen shillings to John Cripps, the ironmaster of Horsted Keynes Furnace, to cast him a fireback weighing one hundredweight and three quarters, with GMS, his and his wife’s initials, on it. Two months later he paid ten shillings for another fireback, this time bearing the arms of the Michelborne family, who held the advowson of Moore’s church. The difference in price could be accounted for by the weight of iron, as Moore had paid a tip to the founder, but Cripps had discounted the cost in lieu of paying tithes. However, Moore had to wait until a batch of pot-casting was due before the second fireback could be made, which suggests that at some furnaces the ironworkers employed were only used to casting rough iron sows, and were not sufficiently skilled in the more delicate preparation of moulds and casting of decorative ironwork. That the fireback was to be cast ‘in Mr Michelbornes mould’ seems to imply that the term ‘mould’ was synonymous with the terms ‘model’ or ‘pattern’ at the time. It is certainly evident from the range of firebacks recorded by the author that the quality of their production varied considerably and that the skill of the ironworkers responsible for their moulding and casting was similarly varied. Hans Schubert observed that the output of castings was higher at furnaces where guns and shot were produced, presumably because they employed a more highly skilled workforce.56
The price charged for firebacks was, as noted above, largely based on the weight of iron. Ten years earlier than the Rev. Moore’s purchase, Sir James Hope, a Scottish lead producer, had visited Barden Furnace, near Tonbridge, one of John Browne’s works, and had enquired of the price per hundredweight of chimney backs.57 He was quoted 20 shillings by the workmen, which equates reasonably with the discounted price paid by Moore. However, in 1661 George Sitwell a Derbyshire ironmaster, was selling chimney plates made at Foxbrooke Furnace at 8 shillings a hundredweight.58 By the 1710s, the backs produced at furnaces operated by the Foley Ironworking Partnership in Gloucestershire and Herefordshire were generally being costed at 10 shillings a hundredweight.59 The cost of the 50 firebacks for Boughton House in the 1740s was £48, which averages out at about 6s 10d a hundredweight.60 Their shipping from one of the ports on Morecambe Bay to King’s Lynn in Norfolk cost 10 shillings a ton, and with handling charges added for the loading and unloading as they were brought from there to their final destination, the bill was £6 13s 6d.17

Ironworks accounts occasionally provide some insight into the wages paid to ironworkers who cast firebacks. Ironworkers were paid according to the weight of the iron they cast. In a memorandum preceding the accounts of Beech and Robertsbridge furnaces in Sussex in the 1720s, the founder or his deputy were to be paid an additional 6s 8d a ton, on top of their weekly wages of 14 shillings and 9s 4d respectively, for ladling iron when casting firebacks.61 At Waldron, in the same county, John Wimble, the founder, was paid between a shilling and 2s 6d each for firebacks of three different sizes.62 The extra work required to arrange the decorative elements in the fireback moulds was represented in the difference between the payments for casting them and for casting simple plates for lining forge hearths, which was a mere 6 pence a plate. The same rate applied at Heathfield Furnace in 1758 where Thomas Cavie the founder was paid 3 shillings for casting three backs weighing just over 6 hundredweight for John Mears Fagg, a local landowner, who was charged £4 10s 6d for the order (for one of which see Fig. 19).63 Such accounts are rare evidence of the people who cast firebacks, most of whom are anonymous.
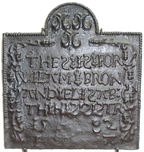
Occasionally, however, the makers of firebacks marked their products. A Tudor armorial back (Fig. 2) bears the unambiguous inscription – Made in Sussex by John Harvo. He was known to have been active as founder at Pounsley Furnace in Framfield between 1547 and 1562. Having his full name is unique. The most that can usually be hoped for are sets of initials, and where the same initials appear on a series of stylistically related backs formed from whole carved patterns, they are likely to be those of the pattern maker. However, in a few instances founders placed their initials on their work. Four firebacks produced in 1582, decorated with hand-placed lettering and other stamps, carry the initials IA (see Fig. 20); their attribution by Mark Antony Lower, and subsequently by Ernest Straker, to a John Apsley is unlikely to be correct.64

An early-seventeenth century group of firebacks bear the repeated stamp of a shield of the Elizabethan judge William Ayloffe and his wife (Fig. 21). Most are undated but the few that do carry a date more often than not include the initials CT.65 Their distribution in the west Kent area coincides, both geographically and chronologically, with the career of the founder Charles Tyler, suggesting that he was responsible for their production and that he retained possession of the armorial stamp when he moved from employment at one furnace to another.66
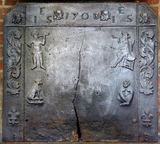
Retention of distinctive decorative stamps by the founder also occurred with a later group of backs with the initials IB at the base. Cast between 1703 and 1710, their geographical distribution and decoration that could be associated with the Bristol tobacco trade suggests that they were produced in the Forest of Dean (see Fig. 22). However two further examples of this founder’s work were cast in 1721 at Sowley Furnace, near Beaulieu in Hampshire. From 1717 Sowley had been operated by John White, an ironmaster from Monmouth, on the edge of the Forest of Dean, and it is evident from the names in the parish register of Beaulieu in that period that several Welsh ironworkers had come to work at the furnace, suggesting that IB was among those who had relocated to Hampshire.67
While the identity of IB remains a mystery, WR, whose initials are on the final batch of firebacks cast in 1813 at Ashburnham Furnace, in Sussex, is known (Fig. 23). Recalling that occasion in old age, William Hobday who, as a 10-year-old boy, had been one of the workers at the furnace, named the founder as William Rummins.68
While Giles Moore could call in at his local furnace to order a couple of firebacks for the chimneys of his house, householders in areas away from the main iron-production regions had to resort to local ironmongers to source firebacks from further afield. References as early as 1565 to firebacks in inventories of the property of citizens in Exeter, several day’s journey from the nearest iron production area at that time, are evidence of availability.69 Just such a market was catered for by the brothers Andrew and James Trubshaw, who placed a large order for firebacks with George Sitwell in 1664. Andrew Trubshaw had an ironmongery business by Cole Harbour Stairs, off Thames Street, west of London Bridge. He and his brother, who had a similar business in Birmingham, asked Sitwell to cast 30 tons of firebacks, to be delivered to their kinsman, Samuel Trubshaw, at Bawtry on the Great North Road, which had navigable access to the River Idle, a tributary of the Trent. Three ‘moulds’ (i.e. patterns) were sent from London to Sitwell’s furnace at Foxbrooke, north-east of Chesterfield in Derbyshire: the king’s arms, the flower pot, and the phoenix. Sitwell went ahead and had the backs cast, producing 362 for dispatch to the Trubshaws. The Trubshaws were difficult customers, attempting to reduce the order after the firebacks had been cast, and then failing to pay for nearly two years.70
The ubiquity of firebacks bearing the Stuart royal arms makes identification of the exact design of one of the types of backs that Sitwell cast for the Trubshaws nigh on impossible. Designs bearing vases of flowers are also not uncommon. However, the phoenix is a feature of a very limited number of designs, and identification may be easier. This particular case serves to indicate that both firebacks and the patterns that were used to form the moulds from which they were cast could be made considerable distances from where they were sold, and introduces an important caveat that assumptions of the local provenance of firebacks can be, and often are, entirely without foundation. The production of firebacks for a specific dealer is also noted in the accounts for Bishopswood Furnace in Gloucestershire in 1707, from where 35 firebacks weighing more than two tons were dispatched to Thomas Morgan, a Bristol ironmonger.71
Private arrangements to acquire firebacks by residents of areas distant from ironworks, but not involving ironmongers or other wholesalers, also existed. The Elizabethan judge, John Ayloffe, mentioned above and a resident of Hornchurch in Essex, in all probability will have had to arrange with a Kent iron founder to produce for him a fireback bearing his and his wife’s shield. A century and a half later, Sir Thomas Bramstone of Roxwell, also in Essex, made use of his mother’s family connections to acquire two firebacks from Heathfield Furnace, nearly 100 miles away in Sussex, in 1740. His second cousin was the ironmaster John Fuller who had the firebacks delivered to a warehouse close to the Thames at Wapping from where a hoyman had to ship them round to Maldon.72
Excise duties were levied on firebacks. The customs charge imposed by the sheriffs of Bristol has already been noted. In Scotland in 1611 backs, confusingly, were listed twice, first as chimney backs, attracting duties of £3 and £6, respectively, per item, and then as iron backs for chimneys at 40 shillings and £4.73 These duties were effectively double the cost of production. In June 1657 the Commonwealth parliament passed an act which levied 3 pence on every hundredweight of firebacks, among other cast wares, payable by the maker or founder.74 At the Restoration Charles II was granted a subsidy from imported goods, which included firebacks; small ones were charged 6s 8d and large ones 13s 4d though, as with the Scottish duty, actual sizes were not specified.75 Presumably the same definition applied in 1690 when an additional rate of 1s 2d and 2s 4d to small and large backs respectively was applied.76
These last three pieces of legislation recognised that a significant source of firebacks in the second half of the seventeenth century was the Netherlands. In his weekly digest of trade data and statistics, John Houghton noted that in the year 1695 1,516 chimney backs were imported into England from there, remarking,
And although Holland be a country that (for ought I can learn) has neither mine, nor fewel to work mineral with, yet ‘tis very few of this catalogue that comes not from thence, especially of those that are most manufactur’d, and of greatest value.77
The importation of backs through Antwerp in the 1560s, noted above, may have been an indication of the relatively small indigenous trade in firebacks at that time, but by the 1690s the range of backs produced in the iron-production regions in England and Wales indicated an adequate, if modest, native supply. What this new wave of imports reflects is a demand for a new style of fireback that was being produced using Dutch-inspired patterns in the Siegerland area of north Germany (e.g. Fig. 24). Originally destined for the Dutch market, their popularity in Britain was stimulated by the accession of William, Prince of Orange, the consort and co-sovereign of Queen Mary II, in 1689. Demand may also have been particularly London-based initially. Rebuilding in the city, following the Great Fire of London, resulted in smaller fireplaces requiring narrower firebacks, for which such imports, or copies made from them, may have been particularly suitable. The trade evidently continued into the reign of Queen Anne, nine chimney backs noted as being imported into London in July 1707 though from where was not stated.78 Chimney backs were also among the imports into Hull around the same time.79 Evidently not only were firebacks being imported from the Low Countries but their patterns were too. An inventory of the stock at the Coalbrookdale ironworks in Shropshire in 1718 includes five ‘Dutch back patterns’ valued at one pound each.80 An illuminating notice in an early London newspaper dates from this period:
On the 13th of this Inst. November [1699], early in the morning, the Warehouse of Jhon Nicole Esq on Mr Jolley’s Stone-Wharf, near White Friars Dock, was broken open, and stolen and carried away from thence by two or more Persons, these Goods, or Iron-wares, viz. 5 Iron Chimney-Backs cast in the figure of Fortune standing naked on a Conchus in the Sea, 6 backs in the figure of a Fox and Crane, 6 Ditto of Juno drawn in a Chariot with Peacocks, 6 of Venus in a Chariot with Doves, 5 Lions rampant, 4 small Fortunes, 3 of Hope with an Anchor, and 5 Hearth-plates … Whoever shall discover the said Person and Wares, so as the same may be recover’d, shall have 40s reward.81
Some of the designs of the firebacks described have decoration typical of the imported types, others, such as Fig. 25, might be English pastiches. The John Nicoll who rented the warehouse may have been the proprietor of the Darvell iron furnace at Mountfield in Sussex; he had several properties in Middlesex and London, and chambers in the Inner Temple. Whether the firebacks stored in the warehouse were imported or cast in an English furnace they would have been destined for sale by a London ironmonger.
By the end of the seventeenth century evidence begins to emerge of the existence of foundries in London supplying a range of cast-iron wares, including firebacks. In 1700 Moses Stringer advertised in the Post Man and Historic Account his stock of ironwork for trade and domestic customers at his foundry in Blackfriars, near Ludgate.82 Between then and the 1730s other founders brought their products to public notice in the newspapers that were proliferating at the time. Among them were George Blatchford, and later Robert Baden, at Bankside in Southwark; William Bowen and Anthony Ireland at White Friars Dock, south of Fleet Street, and William Bowen later on his own account at Marigold Stairs, Southwark; John Wood at the Falcon Foundry, nearby; and Joseph Hambleton at Vaux Hall, Lambeth. These urban foundries used air furnaces wherein pig iron was remelted in heat generated by the height of the chimney rather than requiring a water supply to power bellows as at a blast furnace. Such was the range and similarity of wares advertised by these founders that they may well have been acting as retailers for other producers as well. By the 1730s, however, the day of the fireback was passing, and the same suppliers were advertising grates for coal fires instead.
Firebacks as Church Armorials
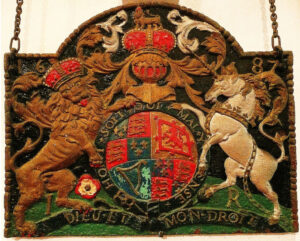
The display of the royal arms in churches had begun in the reign of Edward VI, and possibly earlier. From the Restoration, their installation was widely encouraged. In most instances the arms were either painted on boards or carved from wood or stone. However, in a small number of instances firebacks bearing the royal arms have been placed in churches to fulfil the role, perhaps where earlier arms were lost (they had been ordered to be removed during the Commonwealth) or where the parish had not been able to afford them. At North Cray in Kent, a polychrome fireback of 1687 bearing the arms of James II is suspended over the north aisle (Fig. 26). At Blanchland in Northumberland, a curious fireback is fixed to the wall. Although bearing the initials IR, suggesting James I, the shield, garter and lion supporter are Tudor and can be seen on several firebacks which date from the reign of Henry VIII. More appropriately Jacobean are the firebacks both dated 1618 in St Lawrence’s church at Bigbury in Devon and St George’s near Abergele in North Wales. However, the latter is a painted plaster cast, which was probably installed in the church in the 19th or early-20th century.
A further association between firebacks and church armorials has been noted in three churches in the west of England. In St Cuthbert’s church, at Wells in Somerset, St Stephen’s church in Bristol, and formerly at Temple, or Holy Cross church in Bristol, which was bombed in 1940, the detail of the carved wooden armorials has been found to be so similar to the detail on the series of Stuart royal armorial firebacks made in 1618, two of which were noted above, that it can be confidently asserted that the carver of the church armorials and of the patterns for the firebacks was the same anonymous individual (Fig. 27).83 Subsequently, two other armorials with the same stylistic detail have been identified, one at Spaxton in Somerset and the other formerly from Bath Abbey which is now in a church in Hampshire.
Firebacks as Reward
As might be expected with objects that have remained in situ beyond living memory, firebacks are often the subject of half-remembered associations. Most relate to where a fireback came from, particularly where it was said to have been cast. In a couple of instances, stories allege that firebacks were royal gifts. At Godolphin House, near Helston in Cornwall, a Tudor armorial fireback (Fig. 28) is said to have been a gift from Henry VIII to Sir William Godolphin following the Siege of Boulogne in 1544 where Sir William was master of mines.
At Chawton House, in Hampshire, a variant of the ‘Armada’ fireback (Fig. 29) was said to have been given to the builder of the house, John Knight, by Elizabeth I in gratitude for the £50 that Knight donated to the funds raised towards the defence of the realm at the time of the threat from the Spanish fleet in 1588. Two firebacks at Chawton, both bearing the initials, IK (instead of the usual IFC), are successive copies of an earlier fireback. However, Knight was far from alone in making a donation, it almost being de rigeur for the gentry and aristocracy to respond to the Crown’s appeal, and one might expect a plethora of such gifts to other donors were the Chawton ‘legend’ likely to have any foundation.84
The Historiography of Firebacks
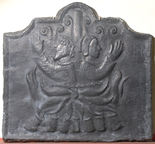
Probably one of the earliest antiquarian references to a fireback is in the pages of the Gentleman’s Magazine in 1788, in connection with an example of the Anne Forster series noted near Norwich.85 In the same year an anonymous correspondent writing in the St James’s Chronicle enquired of a fireback with ‘two bishops burning at stakes thereon’, wondering whether the back was from the reign of Queen Mary or Elizabeth.86 This may be the earliest reference to the ‘Martyr’s’ fireback (Fig. 30).
Mark Anthony Lower, the first writer to consider the history of the iron industry in the Weald, that had come to an end only twenty years before he was writing, included among the illustrations of his paper four firebacks which he had noted in Sussex houses.87 The drawings are of sufficient quality to enable comparison with modern photographs. Other articles and occasional short notices appeared in the pages of the same journal, the Sussex Archaeological Collections, during the following half-century. W. Llewellin, writing in 1862 on the iron industry in South Wales and its connections with that of the Weald, illustrated a fireback of 1553 found there and mentioned others.88
The earliest writer to examine firebacks with more than antiquarian interest was John Starkie Gardner, Keeper of Metalwork at the Victoria & Albert Museum, Kensington, and himself a practising metalworker. He drew upon Lower’s observations in his paper, ‘Iron Casting in the Weald’, much of which dealt with firebacks.89 Taking advantage of developments in printing which enabled him to include photographs, he identified a number of series from the distinctive use of individual stamps. He drew upon examples in the collections at Kensington and of the Sussex Archaeological Society at Lewes, as well as in private hands. While restricted by the limited number of examples available to him, he identified the development in firebacks from the use of stamps to whole patterns, and the introduction of Dutch styles as much because of fashion as of practical necessity. However, his assertion that casting using individual stamps originated in England relied on the mistaken belief that cast iron was available in this country as early as the fourteenth century. Starkie Gardner’s scrapbooks of examples of decorative art include many firebacks, although subsequent research has called into question his identification of many of the personal arms and devices thereon.90 His later treatment of the subject is largely descriptive.91 Following Starkie Gardner’s paper, antiquarian interest in firebacks increased, with correspondents recording their discoveries in the pages of Notes and Queries and similar sections in county journals, and in magazines and books devoted to buildings or decorative arts.
Although referred to by writers in the years immediately following its publication, a now little-known article on firebacks (intended to be the first of a short series) which displayed a breadth of research, as well as a varied selection of examples, is the work of Miller Christy.92 Writing in a society magazine in 1908 Christy, who was a prolific writer on both historical as well as natural history subjects, had evidently had fruitful contact with a number of private collectors as well as museums in both southern England and the near continent, and in a few pages touched upon the social and historical context and distribution of firebacks, before concentrating on their production in the Weald of south-east England and on examples of what he regarded as the earliest of three categories of firebacks, based on groupings proposed by Starkie Gardner.
Perhaps inspired by Starkie Gardner’s work at Kensington, W. Ruskin Butterfield began to assemble a small collection of firebacks at Hastings Museum from farmhouses in the area. In an article in The Connoisseur in 1916, he amplified Starkie Gardner’s classification: Early, being rectangular, often with impressed rope edges and designs formed from individual stamps; Middle, i.e. ones cast from complete patterns, generally of coats of arms; and Late, which were predominantly of the eighteenth century, their height exceeding their width, and with pronounced Netherlandish influence.93 Butterfield’s grouping was adopted by both Ernest Straker, in his monograph on the iron industry in the region,94 and by his successor at the museum, J. Manwaring Baines, who in 1938 wrote a useful booklet about firebacks, reissued 20 years later in a fuller version.95 All three writers also drew, for illustration, upon the large number of firebacks in the museum at Anne of Cleves House in Lewes which became the largest assemblage in the country when it was augmented, in the 1940s, by the private collection of John Every, a local iron-founder.
The most significant writing on firebacks in Britain has been that of H. R. Schubert, who contributed a number of short articles about them to the Journal of the Iron and Steel Institute in the early 1950s, before setting down the most coherent and thoughtful consideration of the subject in his History of the British Iron and Steel Industry.96 Schubert was the first author to review the evidence of the possible influence of continental fireback design and production, and to draw together notices about firebacks in other parts of the British Isles. Simplifying Butterfield’s grouping of firebacks, Schubert described them under two headings: those with separate moveable stamps, and those cast using one-piece patterns. He suggested that fireback production was unlikely to have begun before the 1530s, citing the limited spread of the blast furnace by that time, but arguably attached too much importance to the stylistic significance of individual stamps. His belief that the trailing vine stamp, which occurs with some frequency only on a particular group of Wealden firebacks, was evidence of a motif imported from Wallonia or Lorraine does not bear close scrutiny. However, he was able to show that both English and continental firebacks shared a common heritage in their use of twisted rope, although it is difficult to concur with his assumption that such decoration was confined to early English firebacks when there are examples using rope as late as the 1660s.
Schubert laid stress on the simplicity of many English, whole-pattern designs of the seventeenth century, comparing their boldness to more florid continental ones, although there is little indication that he recognised the stylistic signatures and, in some instances, individual marks that identified particular pattern-makers whose work frequently occurs in some of the larger museum collections. It is, perhaps, curious that Schubert seemed unaware that not only did British iron-founders make use of continental firebacks, imported from the end of the seventeenth century, as patterns, but also native pattern-makers copied their general style, to make distinctly British, baroque designs. While the imported types can be found in collections on both sides of the North Sea, the English and Welsh pastiches are seen only in Britain.
Firebacks have attracted more serious academic interest in Germany than in any other European country, of which the most comprehensive study is that of Karlheinz von den Driesch.97 He also drew upon earlier works, among them those by Albrecht Kippenberger and Sigrid Theisen. In France, Henri Carpentier’s compendious, Plaques de Cheminées, published in 1912, has not been superseded, although its extensive catalogue is largely descriptive. A small number of the firebacks he includes bear English-related designs, but only two can safely be said to have British origins.98 A recent addition in a similar vein has been Philippe Palasi’s Plaques de Cheminées Héraldiques.99 Danish and Norwegian hearth plates, the later ones of which were much influenced by German patterns, have been researched by Arne Nygård-Nilssen,100 and the colonial American production of firebacks and stove-plates, influenced respectively by English and German settlers, has been documented by Henry Mercer.101
Major British collections of firebacks
The oldest major museum collection is that of the Sussex Archaeological Society at Lewes which began with the donation of a fireback in 1852. Further acquisitions to its museum were noted in the pages of early volumes of its published Collections and its holding was considerably enlarged in the 1940s with the bequest of the large private collection of firebacks and other metalwork that had belonged to the local iron founder John Every. The society’s collection, held at Anne of Cleves House in the town and at the other historic properties it owns and opens to the public, numbers about 190 firebacks.
The first fireback donated to the Victoria and Albert Museum in Kensington was in 1892, approximately coinciding with the appointment of John Starkie Gardner as its Keeper of Metalwork. While the bulk of its collection was acquired before the Second World War a small number have been added since, amounting to about 60 in total.
Hastings Museum, in East Sussex, was given its first fireback by its then curator, W. R. Butterfield, in 1901 and he encouraged the accumulation of a modest number over the next quarter of a century. The collection was greatly enhanced in 1952 by the gift of nearly 60 backs that had belonged to the Ade family of Hellingly in East Sussex. The museum now possesses over 80 firebacks.
Visitors to Petworth House in West Sussex will come across a display of firebacks arranged along the corridor in the old servants’ building detached from the main house. These are a collection of over 60, predominantly of continental origin or style, assembled locally by the Mitford family of Pitshill House at Upperton, a few miles to the west of Petworth, and on loan to the National Trust since about 1950 when Pitshill was sold.
Smaller collections numbering no more than 20 backs are held by Brighton Museum, Maidstone Museum and by the National Museum of Wales at St Fagans, near Cardiff.
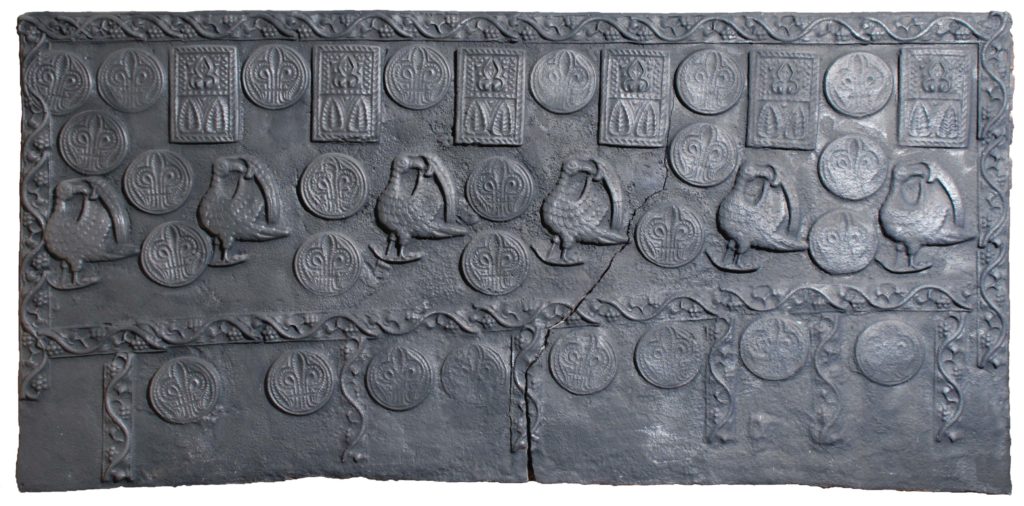
Copyright ©Jeremy Hodgkinson 2010-2025
Footnotes
- R. Lister, Decorative Cast Ironwork in Great Britain (London, G. Bell & Sons, 1960) 28-9.[↩]
- R. Plot, The Natural History of Staffordshire (Oxford, 1686), 164.[↩]
- J. Hodgkinson, The Wealden Iron Industry (Stroud, Tempus, 2008).[↩]
- J. Lucas, A Topographical Description of the Parish of Warton [etc.] (published by the author, 1744).[↩]
- D. Martin and B. Martin, Historic Buildings in Eastern Sussex, no. 1 (Robertsbridge, Rape of Hastings Architectural Survey, 1977), 20-4.[↩]
- Kent History and Library Centre, Maidstone, U455/E1.[↩]
- K. Osborne, Illuminating the Chorus in the Shadows: Elizabethan and Jacobean Exeter 1550-1610, unpublished PhD Thesis, University of Exeter, 2016.[↩]
- M. Reed (ed.), Ipswich Probate Inventories 1583-1631 (Ipswich, Suffolk Records Society, 22, 1981).[↩]
- P. Bracher (ed.), Transcriptions of the Probate Inventories of Crawley, Ifield and Worth in the County of Sussex (Crawley History Group unpublished typescript, 1990).[↩]
- Ledbury Wills and Inventories 1662-1700 (VCH Explore)[↩]
- E. Roberts and K. Parker, Southampton Probate Inventories 1447-1575 (Southampton University Press, Southampton Records Series, 34, 1992), 91.[↩]
- M. Howard and E. Wilson, The Vyne: a Tudor House Revealed (London, The National Trust, 2003), 150.[↩]
- E. M. Bell-Irving, Mayfield: the story of a Wealden village (London, William Clowes, 1903), pp. 177-9.[↩]
- G. R. Batho (ed.), The Household Papers of Henry Percy, ninth Earl of Northumberland, 1564-1632, London, Royal Historical Society, Camden Third Series, 93 (1962), 112-124.[↩]
- G. Isham, ‘Adam Baynes of Leeds and Holdenby, Soldier, Politician, Justice of the Peace, Land Speculator, Demolition Contractor and Prisoner in the Tower’, Northamptonshire Past and Present, 2, 3 (1956), 139-40.[↩]
- A. Fell, The Early Iron Industry of Furness and District (Ulverston, Hume Kitchin, 1908), 35.[↩]
- Boughton House Archives, BN3.6, Box X8701B.[↩][↩]
- Z. E. P. Hudson, Locations, Networks and Cycles: Studying the Everyday Life of Richard Stonley (1520-1600), unpublished PhD thesis, University of Kent, 2017, 105.[↩]
- M. Christy, ‘The Old Flat Hearth and its Appliances, III – The Fire-back’, The Crown, The Court and County Families’ Newspaper, XCIX, Vol. 8, No. 9 (30 May 1908), 384.[↩]
- East Sussex Record Office, PBT 1/1/1/190D and /187A.[↩]
- The National Archives, PROB 11/41/27.[↩]
- R. Garraway Rice, Transcripts of Sussex Wills – Vol. II, Chiddingly to Horsham (Lewes, Sussex Record Society vol. 42, 1938), 265.[↩]
- The National Archives, PROB 11/82/27.[↩]
- The National Archives, PROB 11/230/88.[↩]
- The National Archives, PROB 11/227/265.[↩]
- J. J. Muskett, Suffolk Manorial Families vol. 2 (Exeter, the author, 1908), 92.[↩]
- Gloucester Archives, Gloucester, GDR/18/8/1696/17.[↩]
- R. M. Willatts, Catalogue of Pre-Industrial Revolution Iron Graveslabs in England (1987, rev. J. S. Hodgkinson 2021)[↩]
- R. M. Willatts, ‘Iron Graveslabs: A Sideline of the Early Iron Industry,’ Sussex Archaeological Collections, 125 (1987), 103.[↩]
- J. S. Hodgkinson, ‘A Seventeenth-Century Sussex Woodcarver: the Evidence of Cast Ironwork’, Regional Furniture, 28 (2014), 39-48.[↩]
- J. Hodgkinson, ‘The Anne Forster Firebacks’, Surrey Archaeological Collections, 101 (2018), 99-114.[↩]
- Henry Bush, Bristol Town Duties A Collection of Original and Interesting Documents [Etc.] (Bristol, 1828), pp. 43-83.[↩]
- M. S. Giuseppi, ‘The accounts of the Iron-works at Sheffield and Worth in Sussex, 1546-1549,’ Archaeological Journal, 69 (1912), 300.[↩]
- H. R. Schubert, ‘A Famous English Fireback of 1548,’ Journal of the Iron and Steel Institute, 176 (1954), 36.[↩]
- H. Carpentier, Plaques de Cheminées (Paris, published by the author, 1912), 418.[↩]
- S. Theisen, Der Eifeler Eisenkunstguss im 15 und 16 Jarhundert (Köln, Rheinland-Verlag, 1973), pl. 169; H. Carpentier, Plaques de Cheminées (Paris, published by the author, 1912), 414.[↩]
- W. Llewellin, ‘Sussex Ironmasters in Glamorganshire,’ Archaeologia Cambrensis, 3rd ser., 9 (1863), 90.[↩]
- A. Kippenberger, Die Kunst der Ofenplatten (Düsseldorf, Verlag Stahleisen, 1973), 3.[↩]
- E. Roberts and K. Parker, Southampton Probate Inventories 1447-1575, Vol. 2 (Southampton University Press, Southampton Records Series, 35, 1992), 250.[↩]
- B. Dietz, The Port and Trade of Early Elizabethan London: Documents (London Record Society vol. 8, 1972).[↩]
- P. Williams, The Trading Community of Exeter 1470-1570 with special reference to Merchants and Tailors, PhD thesis, University of Exeter, 2020, 104.[↩]
- [W. C.] Ford, ‘Winthrop in the London Port Books’, Proc. Massachusetts Hist. Soc., 14 (1914), 180.[↩]
- W. Fitzhugh, ‘Letters of William Fitzhugh’, The Virginia Magazine of History and Biography, 1, 3 (Jan 1894), 271.[↩]
- F. W. Camfield, ‘The Maritime Trade of Southampton in the Seventeenth Century’, Papers and Proceedings of the Hampshire Field Club and Archaeological Society, 5, 2 (1906), 144.[↩]
- H. R. Schubert, History of the British Iron and Steel Industry (London, Routledge & Kegan Paul, 1957), 263.[↩][↩]
- A. C. Jones and C. J. Harrison, ‘The Cannock Chase Ironworks, 1590,’ English Historical Review, 93, 368 (July 1978), 805.[↩]
- T. Pennant, A tour in Scotland, and voyage to the Hebrides MDCCLXXII (Chester, John Monk, 1774), 332.[↩]
- The National Archives, SP 16/256, f.142.[↩]
- The National Archives, SP 16/306 ff.180-1.[↩]
- The National Archives, SP 16/264, f.154.[↩]
- The National Archives, SP 16/429, f.156.[↩]
- D. Diderot and J. d’Alembert, Encyclopédie, ou Dictionnaire Raisonné des Sciences, des Arts et des Métiers, Vol. 21, 11 (1765), 21.[↩]
- C. Hart, The Industrial History of Dean (Newton Abbott, David & Charles, 1971), 19.[↩]
- Herefordshire Archives, Hereford, E12/VI/DEf/7 and 13; DFf/1, Foley Partnership Iron Ironworks Accounts.[↩]
- R. Bird, (ed.), Journal of Giles Moore (Lewes, Sussex Record Soc., 68, 1971), 24-5.[↩]
- H. R. Schubert, History of the British Iron and Steel Industry (London, Routledge & Kegan Paul, 1957), 246.[↩]
- P. Marshall, ‘The Diary of Sir James Hope, 1646,’ Miscellany vol. 9, Scottish History Society, 3rd ser., 50 (1958), 149.[↩]
- P. Riden (ed.), George Sitwell’s Letterbook 1662-66 (Chesterfield, Derbyshire Record Society 10, 1985), 235.[↩]
- Herefordshire Archives, Hereford, E12/VI/DFf/2, 4, 7, 9-11.[↩]
- Norfolk Record Office, NRS 20669, Account book of William Folkes of Hillington, esq., to the Duke of Montagu.[↩]
- J. S. Hodgkinson, ‘Notes on early 18th-century memoranda on the making of iron’, Wealden Iron, Bulletin of the Wealden Iron Research Group, 2nd ser., 15 (1995), 13-14.[↩]
- British Library, Add Ms 33154, f.144v.[↩]
- East Sussex Record Office, Brighton, SAS-RF/15/3/35 p.22.[↩]
- M. A. Lower, ‘Iron Works of the County of Sussex,’ Sussex Archaeological Collections, 2 (1849), 217; E. Straker, Wealden Iron (London, Bell, 1931), 418.[↩]
- H. S. Cowper, ‘A Series of Kentish Heraldic Firebacks and the Identification of the Arms’, Archaeologia Cantiana, 29 (1911), 40-6.[↩]
- J. S. Hodgkinson, ‘A series of Kentish firebacks and the possible identification of their founder’, Archaeologia Cantiana, 139 (2018), 312-15.[↩]
- J. S. Hodgkinson, ‘A Series of Distinctive Firebacks’, Base Thoughts, Newsletter of the Antique Metalware Society (Autumn 2020), 7-8.[↩]
- R. F. Whistler, ‘Penhurst: being some account of its Iron Works, Manor House, Church, etc.,’ Sussex Archaeological Collections, 36 (1888), 3.[↩]
- K. Osborne, Illuminating the Chorus in the Shadows: Elizabethan and Jacobean Exeter 1550-1610, unpublished PhD Thesis, University of Exeter, 2016, 731.[↩]
- G. R. Sitwell, ‘A Picture of the Iron trade (in the Seventeenth century),’ Derbyshire Archaeological Journal, 10 (1888), 37-8; P. Riden (ed.), George Sitwell’s Letterbook 1662-66 (Chesterfield, Derbyshire Record Society 10, 1985).[↩]
- Gloucestershire Archives, MF/216, Foley Partnership Accounts.[↩]
- D. Crossley and R. Saville (eds.) The Fuller Letters 1728-1755 (Lewes, Sussex Record Society, 76, 139.[↩]
- J. C. Watson, Scottish Overseas Trade 1597-1645, Vol. 2, Unpublished PhD thesis, University of Edinburgh, 2003, 26, 40.[↩]
- 26 Jun 1657, c.19 & 20, Additional Act for the improvement of the Excise or New Impost.[↩]
- 12 Charles II c.4, Subsidy Act 1660.[↩]
- 2 William and Mary c.4, Taxation Act 1690.[↩]
- J. Houghton, A Collection, for improvement of Husbandry and trade (London, Randall Taylor et al) , 10 Sep 1697.[↩]
- The General Remark on Trade, no. 219, 18-21 Jul 1707.[↩]
- J. E. Williams, ‘Hull, 1700-1835’, in K. J. Allison (ed.), A History of the County of York East Riding: Volume 1, the City of Kingston Upon Hull (London, 1969).[↩]
- A. Raistrick, Dynasty of Iron Founders (Ironbridge Gorge Museum Trust, 1989 ed.), 303.[↩]
- Post Boy, 11-16 Nov 1699.[↩]
- Post Man and the Historic Account, 24-26 Dec 1700.[↩]
- J. Hodgkinson, ‘Church Armorials and Firebacks: Evidence of an Early 17th-Century Woodcarver’, Transactions of the Bristol and Gloucestershire Archaeological Society, 135 (2017), 213-23.[↩]
- see John Knight’s fireback[↩]
- W. Wilkins, ‘Sepulchral Monuments at Norwich’ etc., Gentleman’s Magazine (December 1788), 1046.[↩]
- St James’s Chronicle, or the British Evening Post, 7-9 Aug 1788.[↩]
- M. A. Lower, ‘Iron Works of the County of Sussex,’ Sussex Archaeological Collections, 2 (1849), facing pp. 188, 189 and 217.[↩]
- W. Llewellin, ‘Sussex Ironmasters in Glamorganshire,’ Archaeologia Cambrensis, 3rd ser., 9 (1863), 89-91.[↩]
- J. S. Gardner, ‘Iron Casting in the Weald’, Archaeologia, 56, 1 (1898), 139-62[↩]
- John Starkie Gardner Collection, Victoria & Albert Museum, Archive of Art and Design (AAD/2014/8).[↩]
- J. S. Gardner, Ironwork, Part III (London, HMSO, 1922), 158-68.[↩]
- M. Christy, ‘The Old Flat Hearth and its Appliances, III – The Fire-back’, The Crown, The Court and County Families’ Newspaper, XCIX, Vol. 8, No. 9 (30 May 1908), 383-6.[↩]
- W. R. Butterfield, ‘Old Wealden Firebacks,’ The Connoisseur, 46 (1916), 197-209.[↩]
- E. Straker, Wealden Iron (London, Bell, 1931), 168-74.[↩]
- J. M. Baines, Bygones 3: Wealden Firebacks (Hastings Museum, 1938) and Wealden Firebacks (Hastings Museum 1958).[↩]
- H. R. Schubert, History of the British Iron and Steel Industry (London, Routledge & Kegan Paul, 1957), 256-64.[↩]
- K. von den Driesch, Handbuch der Ofen-, Kamin- und Takenplatten im Rheinland (Köln, Rheinland-Verlag, 1990).[↩]
- H. Carpentier, Plaques de Cheminées (Paris, published by the author, 1912), 419.[↩]
- P. Palasi, Plaques de Cheminées Héraldiques (Paris, Gourcuff-Gradenigo, 2014).[↩]
- A. Nygård-Nilssen, Norsk Jernskulptur (Oslo, Cappelens Forlag, 1944).[↩]
- H. C. Mercer, The Bible in Iron (Doylestown PA, Bucks County Historical Society, 1914, 3rd ed. 1961).[↩]